
Failure analysis
Through a large number of analytical methods and techniques to understand the product manufacturing or application process may occur problems. Compo's engineers have industry-leading engineering expertise designed to understand and solve problems through semiconductor and packaging analysis. Assist with customer returns, reliability failures, manufacturing aftereffects support. Our laboratories operate autonomously, but work with third-party testing organizations around the world to share information and resources.

Failure analysis process
Clearly identify the object of analysis
The first step in failure analysis is to confirm with the customer the analysis object and the background of the failure, understand the situation when the failure occurred, and determine which stage of design, production, inspection, storage, transportation, or use the failure occurred. Retest the failed samples provided by the customer to confirm that the analyzed object has indeed failed and avoid ineffective work.
Determine failure mode
The surface phenomenon or manifestation of failure is the failure mode. Electrical testing and microscopic observation are usually used for preliminary analysis to determine the possible causes of failure phenomena or which part of the failed sample is related. IV curve testing is used to determine whether the electrical parameters match the original data, analyze which part of the failed sample the failure phenomenon may be related to, and observe the appearance under a microscope for completeness, mechanical damage, and corrosion marks. Accurately describe the failure characteristic mode. It can locate electrical (open, short, leak, etc.) or physical (crack, erosion) failure characteristics.
Determine the cause of failure
Based on the failure mode, material properties of failed components, manufacturing process theory and experience, combined with the observed shape, size, position, color, chemical composition, physical structural characteristics and other factors of the corresponding failure site, referring to the stress conditions at the stage of failure occurrence, the possible causes of failure are proposed. Failure may be caused by a series of reasons: design defects, material quality issues, manufacturing process problems, improper transportation or storage conditions, overloading during operation, etc.
Study the failure mechanism
The physical and chemical root cause of failure is called failure mechanism, such as (1) possible failure mechanisms of open circuit: electrical burnout (EOS), electrostatic damage (ESD), metal electromigration, electrochemical corrosion of metals, solder joint detachment, and latch up effect of CMOS circuits. (2) Possible failure mechanisms of leakage and short: particle induced short circuit, dielectric breakdown, PN microplasma breakdown, Si AI interpenetration. The study of failure mechanisms requires a lot of technical support, and our daily work is basically a certification process for failure mechanisms.
Propose preventive measures and design improvement methods
Based on analysis and judgment, propose methods and suggestions to eliminate the occurrence of failures, and provide timely feedback to the design, process, and use.

Report conclusion
Once the analysis is complete, the results are documented in a written report that describes the anomaly in relation to the failure mode and contains sufficient archived content for root cause analysis.
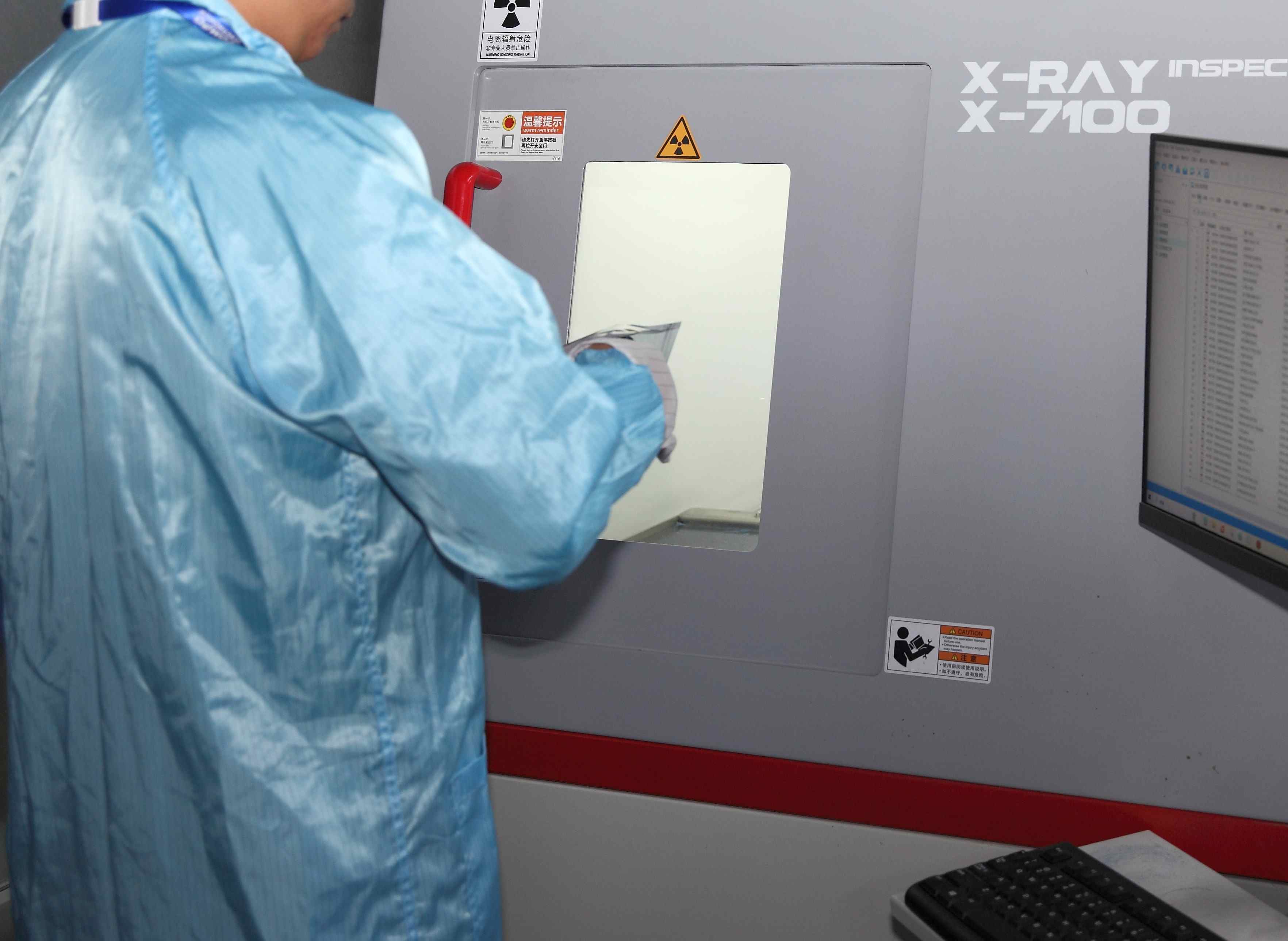